HPMC (hydroksypropylometyloceluloza)jest powszechnie stosowaną domieszką budowlaną i jest szeroko stosowana w zaprawie gipsowej. Jej główne funkcje to poprawa właściwości konstrukcyjnych zaprawy, poprawa retencji wody, zwiększenie przyczepności i dostosowanie właściwości reologicznych zaprawy. Zaprawa gipsowa jest materiałem budowlanym, którego głównym składnikiem jest gips, który jest często stosowany w konstrukcji dekoracji ścian i sufitów.
1. Wpływ dawkowania HPMC na retencję wody w zaprawie gipsowej
Retencja wody jest jedną z ważnych właściwości zaprawy gipsowej, która jest bezpośrednio związana z wydajnością konstrukcji i wytrzymałością wiązania zaprawy. HPMC, jako polimer o dużej masie cząsteczkowej, ma dobrą retencję wody. Jego cząsteczki zawierają dużą liczbę grup hydroksylowych i eterowych. Te hydrofilowe grupy mogą tworzyć wiązania wodorowe z cząsteczkami wody, aby zmniejszyć ulatnianie się wody. Dlatego dodanie odpowiedniej ilości HPMC może skutecznie poprawić retencję wody w zaprawie i zapobiec zbyt szybkiemu wysychaniu zaprawy i pękaniu na powierzchni podczas budowy.
Badania wykazały, że wraz ze wzrostem dawki HPMC, retencja wody w zaprawie stopniowo wzrasta. Jednak gdy dawka jest zbyt wysoka, reologia zaprawy może być zbyt duża, co wpływa na wydajność konstrukcji. Dlatego też optymalną dawkę HPMC należy dostosować do rzeczywistego zastosowania.
2. Wpływ dawkowania HPMC na wytrzymałość wiązania zaprawy gipsowej
Siła wiązania jest kolejnym kluczowym parametrem zaprawy gipsowej, który bezpośrednio wpływa na przyczepność między zaprawą a podłożem. HPMC, jako polimer o dużej masie cząsteczkowej, może poprawić spójność i właściwości wiązania zaprawy. Odpowiednia ilość HPMC może poprawić wiązanie zaprawy, dzięki czemu może ona utworzyć silniejszą przyczepność ze ścianą i podłożem podczas budowy.
Badania eksperymentalne wykazały, że dawka HPMC ma znaczący wpływ na siłę wiązania zaprawy. Gdy dawka HPMC mieści się w pewnym zakresie (zwykle 0,2%–0,6%), siła wiązania wykazuje tendencję wzrostową. Dzieje się tak, ponieważ HPMC może zwiększać plastyczność zaprawy, dzięki czemu może ona lepiej dopasować się do podłoża podczas budowy i zmniejszyć łuszczenie i pękanie. Jednakże, jeśli dawka jest zbyt wysoka, zaprawa może mieć nadmierną płynność, co wpływa na jej przyczepność do podłoża, zmniejszając tym samym siłę wiązania.
3. Wpływ dozowania HPMC na płynność i właściwości konstrukcyjne zaprawy gipsowej
Płynność jest bardzo ważnym wskaźnikiem wydajności w procesie budowy zaprawy gipsowej, szczególnie w przypadku budowy ścian o dużej powierzchni. Dodanie HPMC może znacznie poprawić płynność zaprawy, ułatwiając jej budowę i eksploatację. Charakterystyka struktury cząsteczkowej HPMC umożliwia zwiększenie lepkości zaprawy poprzez zagęszczenie, co poprawia operatywność i wydajność konstrukcyjną zaprawy.
Gdy dawka HPMC jest niska, płynność zaprawy jest słaba, co może prowadzić do trudności w budowie, a nawet pękania. Odpowiednia ilość dawki HPMC (zwykle między 0,2%-0,6%) może poprawić płynność zaprawy, poprawić jej właściwości powlekające i efekt wygładzania, a tym samym poprawić wydajność budowy. Jednakże, jeśli dawka jest zbyt wysoka, płynność zaprawy stanie się zbyt lepka, proces budowy stanie się trudny i może to prowadzić do marnotrawstwa materiału.
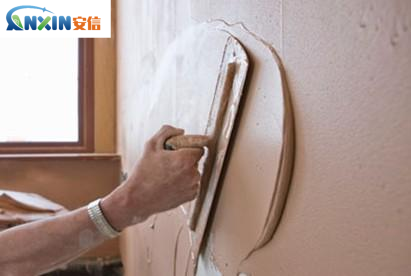
4. Wpływ dozowania HPMC na skurcz suszący zaprawy gipsowej
Skurcz podczas wysychania jest kolejną ważną właściwością zaprawy gipsowej. Nadmierny skurcz może powodować pęknięcia na ścianie. Dodatek HPMC może skutecznie zmniejszyć skurcz podczas wysychania zaprawy. Badanie wykazało, że odpowiednia ilość HPMC może zmniejszyć szybkie parowanie wody, łagodząc w ten sposób problem skurczu podczas wysychania zaprawy gipsowej. Ponadto struktura molekularna HPMC może tworzyć stabilną strukturę sieciową, co dodatkowo poprawia odporność zaprawy na pęknięcia.
Jednakże, jeśli dawka HPMC jest zbyt wysoka, może to spowodować, że zaprawa będzie wiązać przez dłuższy czas, co wpłynie na wydajność konstrukcji. Jednocześnie, wysoka lepkość może powodować nierównomierne rozprowadzanie wody podczas budowy, co wpłynie na poprawę skurczu.
5. Wpływ dozowania HPMC na odporność na pękanie zaprawy gipsowej
Odporność na pękanie jest ważnym wskaźnikiem oceny jakości zaprawy gipsowej. HPMC może poprawić odporność na pękanie poprzez poprawę wytrzymałości na ściskanie, przyczepności i wytrzymałości zaprawy. Dodając odpowiednią ilość HPMC, można skutecznie poprawić odporność zaprawy gipsowej na pękanie, aby uniknąć pęknięć spowodowanych przez siły zewnętrzne lub zmiany temperatury.
Optymalna dawka HPMC wynosi zazwyczaj od 0,3% do 0,5%, co może zwiększyć wytrzymałość strukturalną zaprawy i zmniejszyć pęknięcia spowodowane różnicą temperatur i skurczem. Jednakże, jeśli dawka jest zbyt wysoka, nadmierna lepkość może spowodować zbyt wolne utwardzanie zaprawy, co wpłynie na jej ogólną odporność na pęknięcia.
6. Optymalizacja i praktyczne zastosowanie dawkowania HPMC
Z analizy powyższych wskaźników efektywności wynika, że dawkowanieHPMCma znaczący wpływ na wydajność zaprawy gipsowej. Jednak optymalny zakres dawkowania jest procesem równowagi, a dawkowanie zwykle zaleca się na poziomie od 0,2% do 0,6%. Różne środowiska budowlane i wymagania użytkowe mogą wymagać dostosowania dawkowania w celu uzyskania najlepszej wydajności. W zastosowaniach praktycznych, oprócz dawkowania HPMC, należy wziąć pod uwagę inne czynniki, takie jak proporcja zaprawy, właściwości podłoża i warunki budowy.
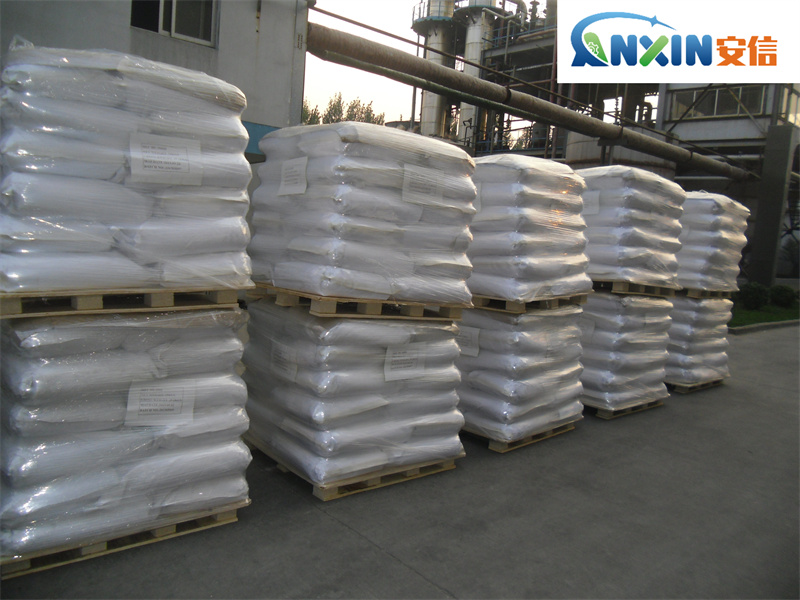
Dawkowanie HPMC ma znaczący wpływ na wydajność zaprawy gipsowej. Odpowiednia ilość HPMC może skutecznie poprawić kluczowe właściwości zaprawy, takie jak retencja wody, wytrzymałość wiązania, płynność i odporność na pękanie. Kontrola dawkowania powinna kompleksowo uwzględniać wymagania dotyczące wydajności konstrukcyjnej i końcowej wytrzymałości zaprawy. Rozsądne dawkowanie HPMC może nie tylko poprawić wydajność konstrukcyjną zaprawy, ale także poprawić długoterminową wydajność zaprawy. Dlatego w rzeczywistej produkcji i budownictwie dawkowanie HPMC powinno być zoptymalizowane zgodnie ze szczególnymi potrzebami, aby osiągnąć najlepszy efekt.
Czas publikacji: 16-12-2024