CMC (karboximetylcellulosa) är ett viktigt textilbearbetningsmedel och har ett brett spektrum av applikationer i textilbearbetningsprocessen. Det är ett vattenlösligt cellulosaderivat med god förtjockning, vidhäftning, stabilitet och andra egenskaper, och används ofta i textiltryck, efterbehandling, färgning och andra länkar.
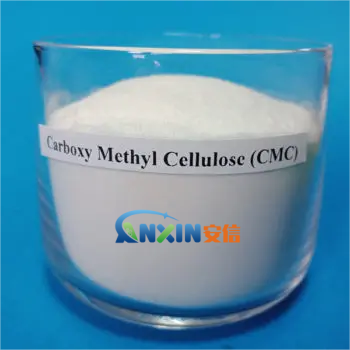
1. CMC:s roll i textilbearbetning
Förtjockande effekt
CMC, som ett naturligt polymerförtjockningsmedel, används ofta för att öka viskositeten hos flytande efterbehandlingsmedel vid textilbehandling. Det kan förbättra vätskans flytbarhet och göra den mer jämnt fördelad på textilytan, och därigenom förbättra efterbehandlingseffekten. Dessutom kan den förtjockade efterbehandlingsvätskan bättre fästa vid textilfiberns yta, förbättra effektiviteten hos efterbehandlingsmedlet och minska förbrukningen av efterbehandlingsmedlet.
Förbättra känslan och mjukheten i tyget
CMC kan förbättra tygets mjukhet genom att bilda en tunn film som täcker fiberytan. Speciellt på tyger som behandlats med CMC kommer känslan att bli mjukare och mer behaglig, vilket uppfyller moderna konsumenters krav på känslan av textilier. Detta är en viktig tillämpning av CMC i textilbehandling, vilket gör det till ett vanligt val för mjuk efterbehandling av textilier.
Förbättra fläckbeständigheten hos tyger
CMC kan förbättra tygytans hydrofilicitet och bilda en skyddande film på tygytan, vilket inte bara effektivt kan förhindra fläckpenetrering utan också förbättra tygets tvättprestanda. I textilfinish hjälper appliceringen av CMC till att förbättra tygernas fläckbeständighet, särskilt vid behandling av vissa avancerade tyger eller lätt smutsiga tyger.
Främja färgnings- och tryckeffekter
CMC används ofta som förtjockningsmedel i processen för textiltryck och tryck. Det kan justera viskositeten hos färgämnen och tryckslam för att göra dem mer jämnt fördelade på textiliernas yta, förbättra noggrannheten vid färgning och tryckning och färgmättnaden. Eftersom CMC har bra färgspridning kan det också hjälpa färgämnen att penetrera bättre i fibern, förbättra färgningslikformigheten och djupet.
Förbättra tvättbarheten av tyger
Efterbehandlingseffekten av CMC är inte begränsad till behandlingen av tygytan, utan förbättrar också tygets tvättbarhet. I många efterbehandlingsprocesser kan filmskiktet som bildas av CMC behålla sin efterbehandlingseffekt efter att tyget har tvättats många gånger, vilket minskar avklingningen av efterbehandlingseffekten. Tyger som behandlats med CMC kan därför ofta bibehålla efterbehandlingseffekten under längre tid efter tvätt.
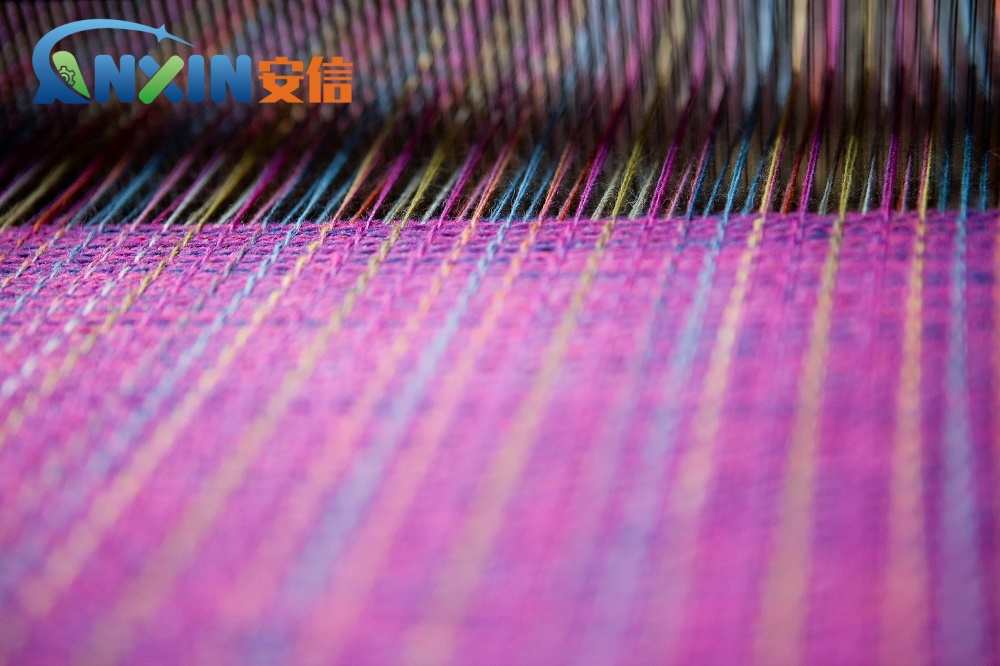
2. Tillämpning av CMC i olika efterbehandlingsprocesser
Mjukgörande efterbehandling
I den mjukgörande efterbehandlingen av textilier kan CMC, som ett naturligt förtjockningsmedel, avsevärt förbättra tygernas mjukhet och komfort. Jämfört med traditionella mjukgörare har CMC bättre miljöskydd och stabilitet, så det används ofta i textilier med höga miljöskyddskrav, såsom babykläder, sängkläder etc.
Anti-rynk finish
CMC kan bilda starka vätebindningar med cellulosa och protein, så det har en viss effekt i anti-rynk finish. Även om anti-rynkeffekten av CMC inte är lika bra som vissa professionella anti-rynk efterbehandlingsmedel, kan den fortfarande förlänga tygets planhet genom att minska friktionen på fiberytan och förbättra tygets rynkbeständighet.
Efterbehandling av färgning
I färgningsprocessen tillsätts ofta CMC till färgen som ett förtjockningsmedel, vilket kan öka färgämnets vidhäftning, förbättra fördelningen av färgämnet på fibern och göra färgningsprocessen mer enhetlig. Tillämpningen av CMC kan avsevärt förbättra färgningseffekten, speciellt vid färgning med stor yta eller komplexa fiberegenskaper, är färgningseffekten särskilt framträdande.
Antistatisk finish
CMC har också en viss antistatisk effekt. I vissa syntetfibertyger är statisk elektricitet en vanlig kvalitetsbrist. Genom att lägga till CMC kan den statiska elektricitetsackumuleringen av tyger effektivt reduceras, vilket gör tygerna mer bekväma och säkra. Antistatisk ytbehandling är särskilt viktig, särskilt i textilier som används i elektroniska produkter och precisionsutrustning.
3. För- och nackdelar med CMC i textilbearbetning
Fördelar
Miljövänlig
CMC är en högmolekylär förening av naturligt ursprung. Dess tillverkningsprocess är inte beroende av skadliga kemikalier, så dess tillämpning i textilfinish är mycket miljövänlig. Jämfört med vissa traditionella syntetiska efterbehandlingsmedel har CMC lägre toxicitet och mindre förorening av miljön.
Nedbrytbarhet
CMC är ett biologiskt nedbrytbart material. Textilier som behandlats med CMC kan sönderdelas bättre efter att ha kasserats, med mindre belastning på miljön, vilket uppfyller kraven på hållbar utveckling.
Hög säkerhet
CMC är giftfritt och ofarligt för människokroppen, så det kan användas i stor utsträckning i textilier för spädbarn, medicinska och andra höga standardkrav, med hög säkerhet.
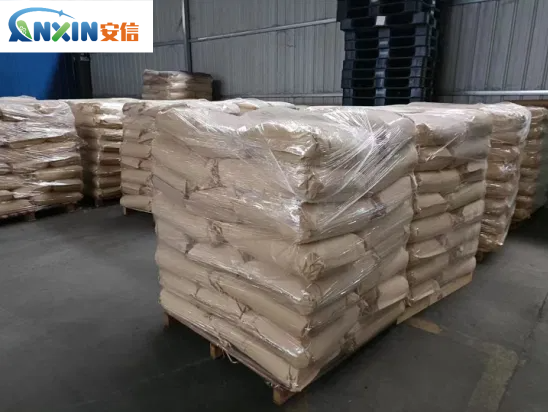
Bra vidhäftning
CMC kan bilda en stark vidhäftning med fibrer och därigenom effektivt förbättra efterbehandlingseffekten och minska slöseriet med efterbehandlingsmedel.
Nackdelar
Påverkas lätt av fukt
CMC absorberar lätt fukt och expanderar i en fuktig miljö, vilket resulterar i en minskning av dess efterbehandlingseffekt. Därför bör särskild uppmärksamhet ägnas åt dess stabilitet när den används i en fuktig miljö.
Höga krav på processteknik
Även omCMC har en god appliceringseffekt vid efterbehandling, dess förtjockning och stabilitet påverkas lätt av processförhållanden. Därför, i praktiska tillämpningar, måste parametrar som temperatur, pH-värde och koncentration kontrolleras strikt.
CMC har visat sina många fördelar inom textilbearbetning och spelar en viktig roll vid förtjockning, mjukgöring, antifouling och färgning av ytbehandling. Med de allt strängare miljöbestämmelserna och den ökande efterfrågan från konsumenter på miljövänliga produkter, gör CMC:s naturlighet och nedbrytbarhet att den har breda tillämpningsmöjligheter inom textilindustrin. I praktiska tillämpningar måste dock vissa tekniska problem fortfarande lösas, såsom fuktens inverkan och finkontroll av processteknik, för att ytterligare förbättra dess efterbehandlingseffekt och appliceringsstabilitet.
Posttid: Jan-06-2025