Hydroxypropyl Methylcellulose (HPMC) is a non-ionic cellulose ether, which is widely used in building materials, especially in repair mortar. As a high-performance additive, HPMC is mainly used as a water retainer, thickener, lubricant and binder, and has obvious advantages in improving the performance of repair mortar.
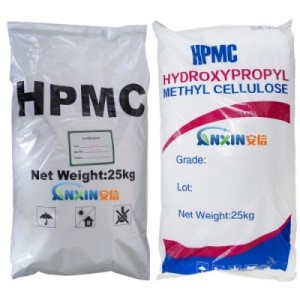
1. Basic characteristics of HPMC
HPMC is a polymer compound modified from natural cellulose through a series of chemical reactions. Its molecular structure contains groups such as methoxy (-OCH₃) and hydroxypropyl (-CH₂CHOHCH₃). The presence of these substituents gives HPMC good solubility and stability, allowing it to quickly dissolve in cold water to form a transparent viscous liquid. It has good thermal stability, enzymatic stability and strong adaptability to acids and alkalis, and is widely used in building materials, coatings, medicine, food and other industries.
2. The role of HPMC in repair mortar
Improve water retention
After adding HPMC to the repair mortar, its excellent water retention performance can significantly delay water loss and ensure sufficient cement hydration. This is especially important for thin-layer construction or high-temperature dry environments, which helps prevent problems such as cracking and delamination, and improves the density and strength development of the mortar.
Improve workability
HPMC can effectively enhance the lubricity and workability of the mortar, making the repair mortar smoother during the application process, easier to operate and form. Its lubricating effect reduces tool resistance during construction, which helps to improve construction efficiency and surface finish.
Improve bonding performance
Repair mortar is often used to repair old base surfaces, requiring good bonding between the mortar and the base. The thickening effect of HPMC enhances the bonding between the mortar and the base, reducing the risk of hollowing and falling off, especially when constructing in special parts such as vertical surfaces or ceilings.
Controlling consistency and anti-sagging
The thickening effect of HPMC can effectively control the consistency of mortar, making it less likely to sag or slip when applied on vertical or inclined surfaces, and maintaining the stability of mortar in the early stages of forming. This is essential for improving construction quality and achieving fine repairs.
Enhanced crack resistance
Since HPMC improves the water retention and flexibility of mortar, it can slow down the shrinkage process, thereby effectively inhibiting the formation of shrinkage cracks and improving the overall durability of the repair layer.
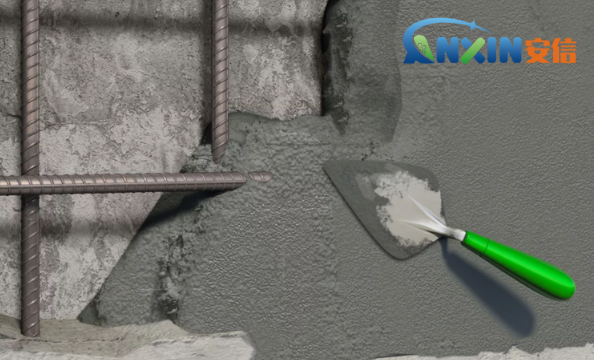
3. Application practice and dosage recommendations
In actual applications, the dosage of HPMC is generally 0.1% to 0.3% of the weight of the mortar. The specific dosage needs to be adjusted according to the type of mortar, construction environment and required performance. Insufficient dosage may not play its due role, while excessive dosage may cause the mortar to be too thick, prolong the setting time, and even affect the final strength.
To achieve the best effect, it is recommended to use it in combination with other additives such as redispersible latex powder, water reducer, anti-cracking fiber, etc., and optimize the formula design according to the construction process and requirements.
The application of HPMC in repair mortar has become an important means to improve product performance. Its excellent water retention, thickening, workability and adhesion not only improve the use effect of repair mortar, but also provide technical support for repair construction in complex environments. As the construction industry continues to increase its requirements for the performance of repair materials, the application value of HPMC will become more prominent, and it will be an indispensable key component in the future high-performance mortar system.
Post time: Apr-04-2025