CMC (Carboxymethyl Cellulose) is a chemical additive widely used in the oil drilling industry, mainly as a thickener and stabilizer for drilling fluids. Its impact on drilling efficiency is multifaceted and can be discussed from the perspectives of improving drilling fluid performance, reducing problems during the drilling process, and optimizing the drilling process.
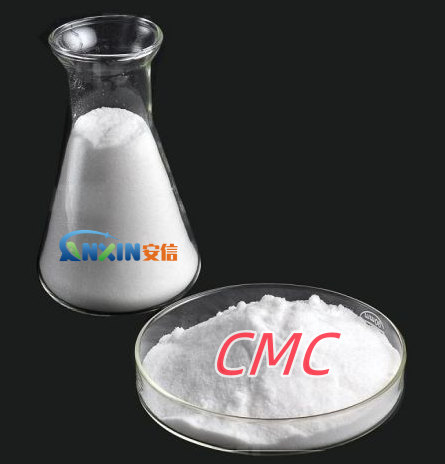
1. Basic functions of CMC
thickening effect
CMC can significantly increase the viscosity of drilling fluid. This property is crucial for drilling operations because the thickened drilling fluid can provide better carrying capacity and transport capabilities, helping to remove cuttings from the wellbore and prevent their deposition. At the same time, higher viscosity helps maintain good suspension in complex formations and prevents cuttings from clogging the wellbore.
liquid stability
CMC has strong water solubility and good temperature and salt resistance, which allows it to function stably under different geological conditions. Its excellent chemical stability and lubrication properties reduce various problems caused by instability of drilling fluid during the drilling process, such as mud precipitation, gas escape, etc.
Reduce fluid loss of water-based mud
Through synergy with other components, CMC can effectively reduce the filter loss of drilling fluid, thereby preventing water from entering the underground layer, reducing damage to surrounding rock formations, protecting the well wall, and thus improving drilling efficiency.
2. The specific impact of CMC on drilling efficiency
Improve the cleaning performance of drilling fluids
During the drilling process, the friction between the drill bit and the formation will produce a large amount of cuttings. If they cannot be removed in time, it will cause interference to the drilling operation. CMC enhances the suspension and carrying capacity of drilling fluid, which can efficiently bring these cuttings out of the wellhead to ensure the cleanliness of the wellbore. This function is especially important for complex well types such as deep wells, ultra-deep wells, and horizontal wells. It can effectively avoid problems such as wellbore clogging and bit sticking, thereby increasing drilling speed.
Reduce the risk of shaft collapse
In some soft or loose rock formations, one of the primary functions of drilling fluids is to maintain the stability of the wellbore wall. As a thickener, CMC can improve the adhesion of drilling fluid, allowing the drilling fluid to form a protective film on the well wall to prevent the well wall from collapsing or the mud from penetrating into the surrounding rock formations. This not only improves the safety of drilling operations, but also reduces downtime caused by well wall instability, thereby improving drilling efficiency.
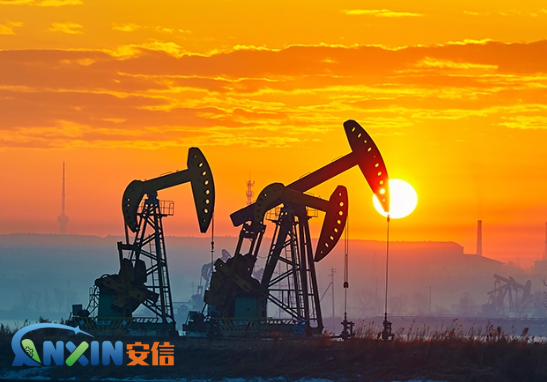
Reduce drilling fluid losses
During the drilling process, drilling fluids may penetrate into the underground formation, especially in areas where the rock has high porosity or fractures. CMC can effectively control the fluid loss of drilling fluid and reduce the loss of drilling fluid in pores and fractures. This not only helps save drilling fluid costs, but also prevents drilling fluid from being lost too quickly and affecting operations, ensuring that the drilling fluid continues to perform its functions effectively.
Improve drilling efficiency and shorten drilling cycle
Because CMC enhances the performance of the drilling fluid, it performs better in cleaning the wellbore, stabilizing the well wall, and carrying cuttings, thereby reducing various problems encountered during the drilling process and ensuring that the drilling operation can be smoother. and perform efficiently. The stability and cleaning performance of drilling fluid directly affect the progress of drilling. The use of CMC increases the drilling speed, thereby shortening the drilling cycle and reducing the overall operating cost.
3. Application examples and practical effects of CMC
deep well drilling
In deep well drilling, as the drilling depth increases and the wellhead pressure increases, the stability and suspension of the drilling fluid are particularly important. By adding CMC, the viscosity of the drilling fluid can be enhanced, the carrying capacity of cuttings can be improved, and the smooth circulation of the drilling fluid can be ensured. In addition, CMC can effectively reduce time waste caused by well wall collapse and leakage, improving the efficiency of deep well drilling.
High temperature and high pressure formation drilling
In formations with high temperatures and high pressures, drilling fluids need to have high thermal stability and pressure resistance. CMC can not only exert a thickening effect at normal temperature, but also maintain good stability in high temperature environments to avoid the degradation of drilling fluid performance. In practical applications, CMC reduces drilling fluid losses during drilling in such formations and reduces downtime caused by drilling fluid problems.
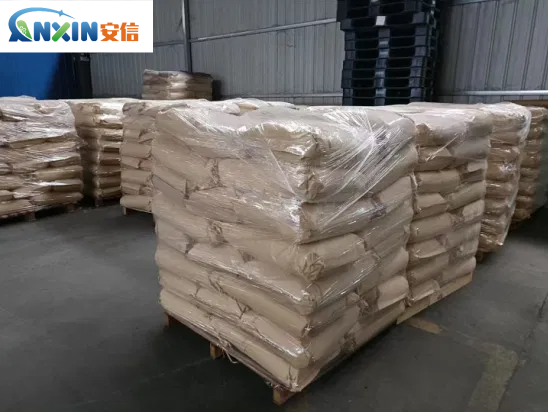
horizontal well drilling
During the drilling process of horizontal wells, since the stability of the well wall and the removal of cuttings are particularly complex, the use of CMC as a thickener has significant effects. CMC can effectively improve the rheology of drilling fluid, help the drilling fluid maintain good suspension and transportation capabilities, so that cuttings can be taken out in time, avoiding problems such as stuck and blockage, and improving the efficiency of horizontal well drilling.
As an efficient drilling fluid additive, CMC's application in the drilling process significantly improves drilling efficiency. By enhancing the viscosity, stability and rheological properties of drilling fluids, CMC plays an important role in cleaning wellbore, reducing well wall collapse, controlling fluid loss, and increasing drilling speed. With the continuous development of drilling technology, CMC has broad application prospects in various complex environments and will continue to play a key role in future drilling operations.
Post time: Dec-21-2024