HPMC (hydroxypropyl methylcellulose) is a commonly used building admixture and is widely used in gypsum mortar. Its main functions are to improve the construction performance of mortar, improve water retention, enhance adhesion and adjust the rheological properties of mortar. Gypsum mortar is a building material with gypsum as the main component, which is often used in wall and ceiling decoration construction.
1. Effect of HPMC dosage on water retention of gypsum mortar
Water retention is one of the important properties of gypsum mortar, which is directly related to the construction performance and bonding strength of mortar. HPMC, as a high molecular polymer, has good water retention. Its molecules contain a large number of hydroxyl and ether groups. These hydrophilic groups can form hydrogen bonds with water molecules to reduce the volatilization of water. Therefore, the addition of an appropriate amount of HPMC can effectively improve the water retention of mortar and prevent the mortar from drying too quickly and cracking on the surface during construction.
Studies have shown that with the increase of HPMC dosage, the water retention of mortar gradually increases. However, when the dosage is too high, the rheology of the mortar may be too large, affecting the construction performance. Therefore, the optimal dosage of HPMC needs to be adjusted according to the actual usage.
2. Effect of HPMC dosage on the bonding strength of gypsum mortar
Bonding strength is another key performance of gypsum mortar, which directly affects the adhesion between the mortar and the base. HPMC, as a high molecular polymer, can improve the cohesion and bonding performance of the mortar. The right amount of HPMC can improve the bonding of the mortar, so that it can form a stronger adhesion with the wall and substrate during construction.
Experimental studies have shown that the dosage of HPMC has a significant effect on the bonding strength of the mortar. When the HPMC dosage is within a certain range (usually 0.2%-0.6%), the bonding strength shows an upward trend. This is because HPMC can enhance the plasticity of the mortar, so that it can better fit the substrate during construction and reduce shedding and cracking. However, if the dosage is too high, the mortar may have excessive fluidity, affecting its adhesion to the substrate, thereby reducing the bonding strength.
3. Effect of HPMC dosage on the fluidity and construction performance of gypsum mortar
Fluidity is a very important performance indicator in the construction process of gypsum mortar, especially in large-area wall construction. The addition of HPMC can significantly improve the fluidity of mortar, making it easier to construct and operate. The characteristics of HPMC molecular structure enable it to increase the viscosity of mortar by thickening, thereby improving the operability and construction performance of mortar.
When the HPMC dosage is low, the fluidity of mortar is poor, which may lead to construction difficulties and even cracking. The appropriate amount of HPMC dosage (usually between 0.2%-0.6%) can improve the fluidity of mortar, improve its coating performance and smoothing effect, and thus improve construction efficiency. However, if the dosage is too high, the fluidity of mortar will become too viscous, the construction process will become difficult, and it may lead to material waste.
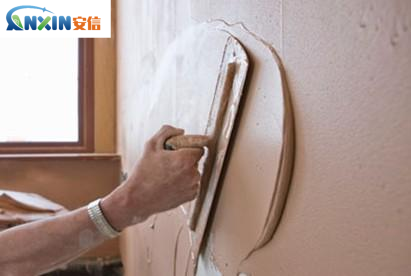
4. Effect of HPMC dosage on drying shrinkage of gypsum mortar
Drying shrinkage is another important property of gypsum mortar. Excessive shrinkage may cause cracks on the wall. The addition of HPMC can effectively reduce the drying shrinkage of mortar. The study found that the appropriate amount of HPMC can reduce the rapid evaporation of water, thereby alleviating the drying shrinkage problem of gypsum mortar. In addition, the molecular structure of HPMC can form a stable network structure, further improving the crack resistance of the mortar.
However, if the dosage of HPMC is too high, it may cause the mortar to set for a longer time, affecting the construction efficiency. At the same time, the high viscosity may cause uneven distribution of water during construction, affecting the improvement of shrinkage.
5. Effect of HPMC dosage on crack resistance of gypsum mortar
Crack resistance is an important indicator for evaluating the quality of gypsum mortar. HPMC can improve its crack resistance by improving the compressive strength, adhesion and toughness of the mortar. By adding an appropriate amount of HPMC, the crack resistance of gypsum mortar can be effectively improved to avoid cracks caused by external force or temperature changes.
The optimal dosage of HPMC is generally between 0.3% and 0.5%, which can enhance the structural toughness of the mortar and reduce cracks caused by temperature difference and shrinkage. However, if the dosage is too high, the excessive viscosity may cause the mortar to cure too slowly, thus affecting its overall crack resistance.
6. Optimization and practical application of HPMC dosage
From the analysis of the above performance indicators, the dosage of HPMC has a significant impact on the performance of gypsum mortar. However, the optimal dosage range is a balance process, and the dosage is usually recommended to be 0.2% to 0.6%. Different construction environments and usage requirements may require adjustments to the dosage to achieve the best performance. In practical applications, in addition to the dosage of HPMC, other factors need to be considered, such as the proportion of mortar, the properties of the substrate, and construction conditions.
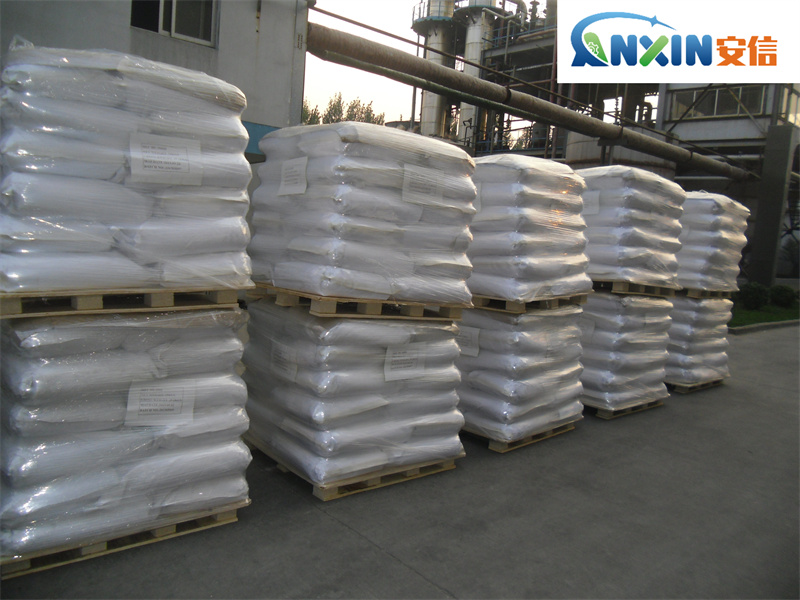
The dosage of HPMC has a significant impact on the performance of gypsum mortar. The appropriate amount of HPMC can effectively improve the key properties of mortar such as water retention, bonding strength, fluidity, and crack resistance. The control of the dosage should comprehensively consider the requirements of construction performance and final strength of mortar. Reasonable HPMC dosage can not only improve the construction performance of mortar, but also improve the long-term performance of mortar. Therefore, in actual production and construction, the dosage of HPMC should be optimized according to specific needs to achieve the best effect.
Post time: Dec-16-2024