The role of CMC (Carboxymethyl Cellulose) in ceramic glazes is mainly reflected in the following aspects: thickening, bonding, dispersion, improving coating performance, controlling glaze quality, etc. As an important natural polymer chemical, it is widely used in the preparation of ceramic glazes and ceramic slurries.
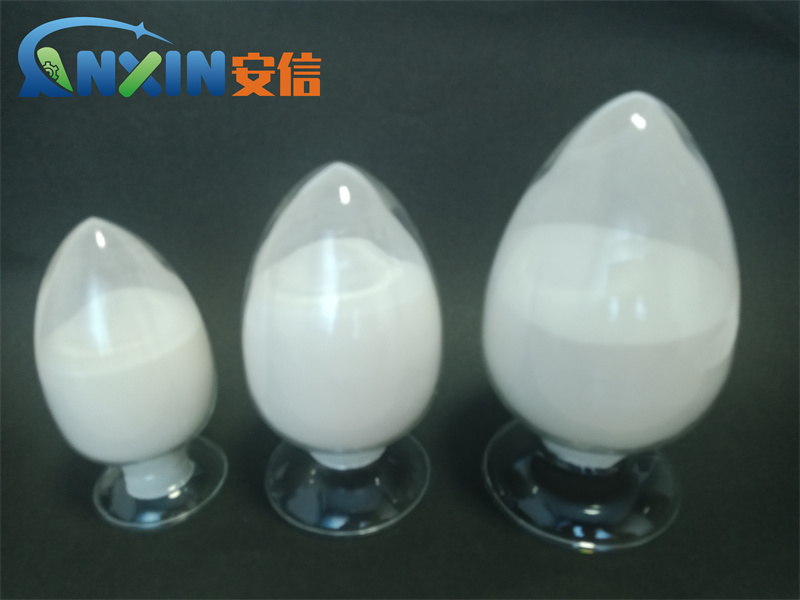
1. Thickening effect
CMC is a water-soluble polymer compound that can form a viscous solution in water. This feature makes its role in ceramic glazes particularly prominent, especially when the viscosity of the glaze needs to be adjusted. Ceramic glazes are usually composed of inorganic powders, glass formers, fluxing agents, etc. The addition of water sometimes causes the glaze to have excessive fluidity, resulting in uneven coating. CMC increases the viscosity of the glaze, making the glaze coating more uniform, reducing the fluidity of the glaze, thereby improving the application effect of the glaze and avoiding problems such as glaze sliding and dripping.
2. Bonding performance
After adding CMC to the ceramic glaze, the CMC molecules will form a certain bonding effect with the inorganic powder in the glaze. CMC enhances the adhesion of glazes by forming hydrogen bonds with water molecules through the carboxyl groups in its molecules and interacting with other chemical groups. This bonding effect enables the glaze to better adhere to the surface of the ceramic substrate during the coating process, reduces the peeling and shedding of the coating, and improves the stability of the glaze layer.
3. Dispersion effect
CMC also has a good dispersing effect. In the preparation process of ceramic glazes, especially when using some inorganic powders with larger particles, AnxinCel®CMC can prevent the particles from agglomerating and maintain their dispersibility in the water phase. The carboxyl groups on the CMC molecular chain interact with the surface of the particles, effectively reducing the attraction between the particles, thereby improving the dispersibility and stability of the glaze. This is of great significance to the uniformity and color consistency of the glaze.
4. Improve coating performance
The coating performance of ceramic glazes is crucial to the quality of the final glaze. CMC can improve the fluidity of the glaze, making it easier to evenly coat the surface of the ceramic body. In addition, CMC adjusts the viscosity and rheology of the glaze, so that the glaze can stably adhere to the surface of the body during high-temperature firing and is not easy to fall off. CMC can also effectively reduce the surface tension of glazes and increase the affinity between glazes and the surface of green bodies, thereby improving the fluidity and adhesion of glazes during coating.
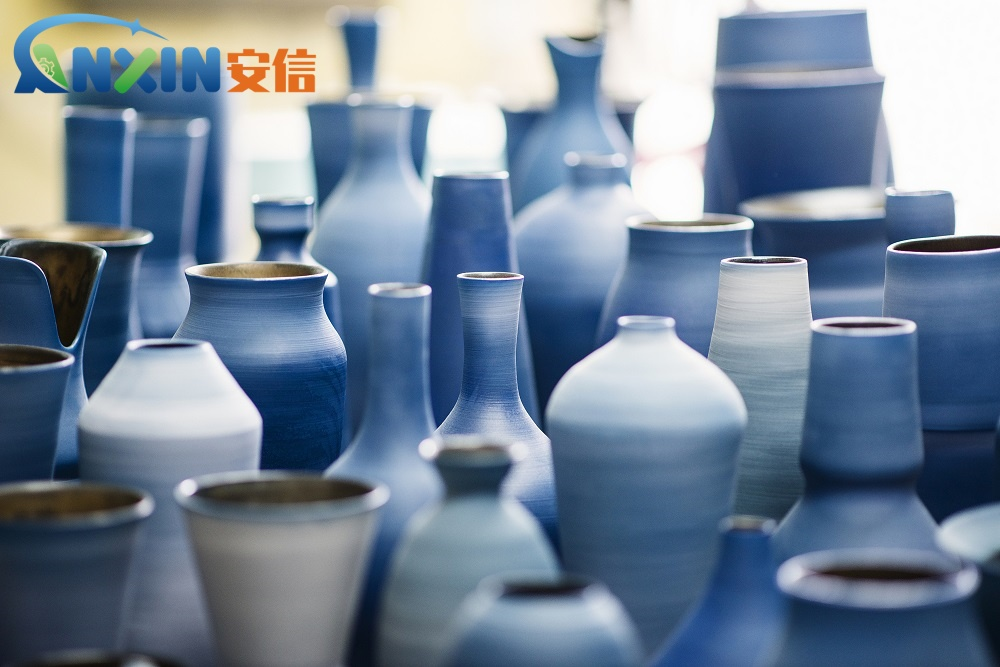
5. Control glaze quality
The final effect of ceramic glazes includes the gloss, flatness, transparency and color of the glaze. The addition of AnxinCel®CMC can optimize these properties to a certain extent. First, the thickening effect of CMC allows the glaze to form a uniform film during the firing process, avoiding defects caused by too thin or too thick glazes. Secondly, CMC can control the evaporation rate of water to avoid uneven drying of the glaze, thereby improving the gloss and transparency of the glaze after firing.
6. Promote the firing process
CMC will decompose and volatilize at high temperatures, and the released gas can have a certain regulating effect on the atmosphere during the glaze firing process. By adjusting the amount of CMC, the expansion and contraction of the glaze during the firing process can be controlled to avoid cracks or uneven contraction on the glaze surface. In addition, the addition of CMC can also help the glaze form a smoother surface at high temperatures and improve the firing quality of ceramic products.
7. Cost and environmental protection
As a natural polymer material, CMC has a lower cost than some synthetic chemicals. In addition, since CMC is biodegradable, it has more environmental advantages during use. In the preparation of ceramic glazes, the use of CMC can not only effectively improve the quality of the product, but also reduce the production cost, which meets the requirements of environmental protection and economy in the modern ceramic industry.
8. Wide applicability
CMC can be used not only in ordinary ceramic glazes, but also in special ceramic products. For example, in high-temperature fired ceramic glazes, CMC can effectively avoid the generation of glaze cracks; in ceramic products that need to have a specific gloss and texture, CMC can optimize the rheology and coating effect of the glaze; in the production of artistic ceramics and craft ceramics, CMC can help improve the delicateness and gloss of the glaze.
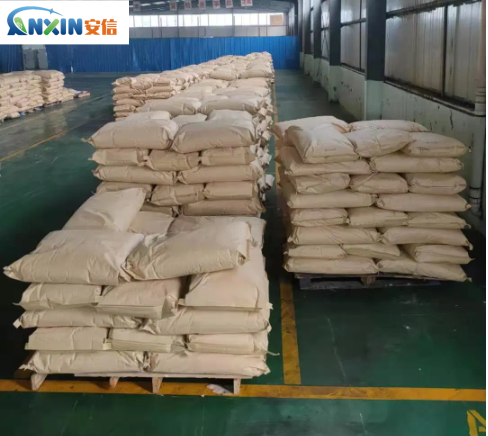
As an additive with multiple functions in ceramic glazes, AnxinCel®CMC has become an indispensable auxiliary material in the ceramic industry. It improves the quality and performance of ceramic glazes through thickening, bonding, dispersion, and improving coating performance, which ultimately affects the appearance, function and firing effect of ceramic products. With the continuous development of the ceramic industry, the application prospects of CMC will be more extensive, and its environmental protection and low-cost advantages also make it play an important role in future ceramic production.
Post time: Jan-06-2025