CMC (sodium carboxymethyl cellulose) is an important water-soluble polymer compound that plays a variety of key roles in deep-sea drilling, especially in the preparation and performance optimization of drilling fluids. Deep-sea drilling is an operation with extremely high technical requirements and harsh environmental conditions. With the development of offshore oil and gas resources, the scale and depth of deep-sea drilling are gradually increasing. As an efficient chemical additive, CMC can improve the efficiency, safety and environmental protection of the drilling process.
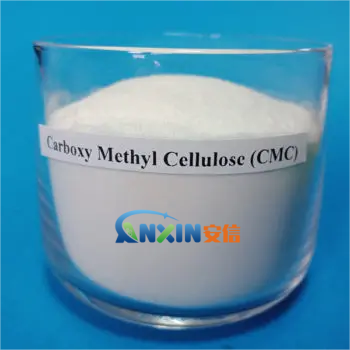
1. Key role in drilling fluid
During deep-sea drilling, drilling fluid plays important functions such as supporting the well wall, cooling the drill bit, removing chips, and maintaining downhole pressure. CMC is an efficient viscosity regulator, rheological agent and thickener, which is widely used in the preparation of drilling fluids. Its main functions are reflected in the following aspects:
1.1 Thickening and adjusting viscosity
In deep-sea drilling, due to the increase in water depth and pressure, the drilling fluid must have a certain viscosity to ensure its fluidity and carrying capacity. CMC can effectively thicken drilling fluid and help maintain the stability of drilling fluid at different depths and pressures. By adjusting the concentration of CMC, the viscosity of drilling fluid can be optimized to ensure that the drilling fluid has appropriate flow characteristics, so that it can flow freely in complex deep-sea environments and prevent problems such as wellbore collapse.
1.2 Improving rheological properties
The rheological properties of drilling fluid are crucial in deep-sea drilling. CMC can improve the fluidity of drilling fluid, making it flow more smoothly underground, reducing the friction between the drill bit and the wellbore wall, reducing energy consumption and mechanical wear during drilling, and extending the service life of drilling equipment. In addition, good rheological properties can also ensure that the drilling fluid can effectively carry cuttings and prevent the accumulation of solid particles in the drilling fluid, thereby avoiding problems such as blockage.
2. Wellbore stability and inhibition of hydrate formation
In the process of deep-sea drilling, wellbore stability is a key issue. Deep-sea areas often face complex geological conditions, such as high pressure, high temperature, and sediment deposition, which may lead to wellbore collapse or drilling fluid loss. CMC helps to enhance the stability of the wellbore wall and prevent wellbore collapse by improving the viscosity and rheological properties of the drilling fluid.
In deep-sea drilling, the formation of hydrates (such as natural gas hydrates) is also an issue that cannot be ignored. Under low temperature and high pressure conditions, natural gas hydrates are easily formed during the drilling process and cause clogging of the drilling fluid. As an efficient hydration agent, CMC can effectively inhibit the formation of hydrates, maintain the fluidity of the drilling fluid, and ensure the smooth progress of drilling operations.
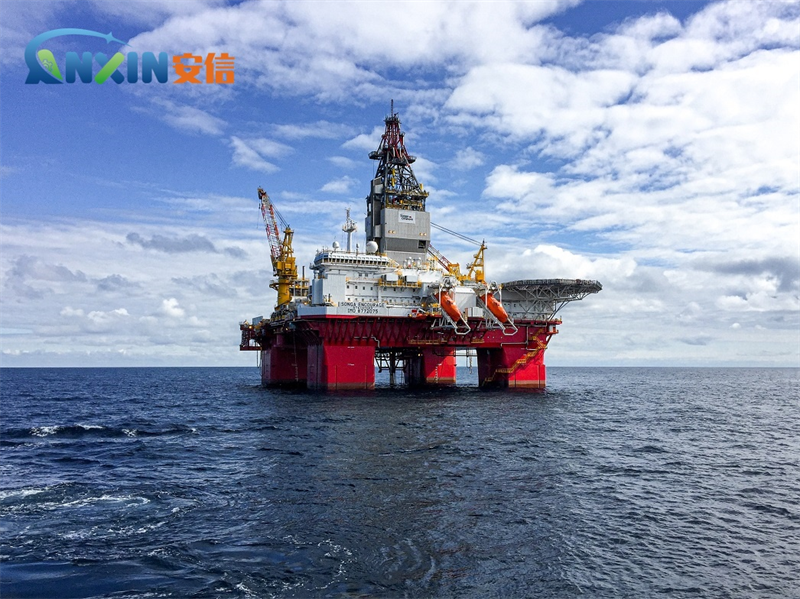
3. Reduce environmental impact
With the increasingly stringent environmental protection requirements, the impact on the environment during deep-sea drilling has received more and more attention. The application of CMC in deep-sea drilling can effectively reduce the emission of harmful substances in the drilling fluid. As a natural material, CMC has good biodegradability and environmental friendliness. Its use can reduce the toxicity of the drilling fluid and reduce pollution to the marine ecosystem.
In addition, CMC can also improve the recycling rate of drilling fluid. By effectively adjusting the performance of the drilling fluid, reducing the loss of the drilling fluid, and ensuring that the drilling fluid can be reused repeatedly, the burden on the marine environment during the drilling process is reduced. This is of great significance for the sustainable development of deep-sea drilling.
4. Improve drilling efficiency and safety
The use of CMC not only improves the performance of deep-sea drilling fluid, but also improves drilling efficiency and operation safety to a certain extent. First, CMC can make drilling fluid better adapt to different geological conditions, reduce the phenomenon of stuck pipe and blockage during drilling, and ensure the smooth progress of drilling operations. Secondly, stable drilling fluid performance can improve drilling accuracy and avoid drilling failures caused by unstable well wall or other factors. In addition, CMC can effectively reduce the risk of downhole pressure fluctuations, reduce dangerous situations such as blowouts and mud spraying that may occur during drilling, and ensure the safety of operations.
5. Cost-effectiveness and economy
Although the application of CMC will increase certain costs, these costs are relatively controllable compared to the improvement in drilling efficiency and safety assurance it brings. CMC can improve the stability of drilling fluid and reduce the need for other chemical additives, thereby reducing the overall cost of drilling fluid. At the same time, the use of CMC can reduce equipment loss and maintenance costs, improve the production efficiency of drilling operations, and thus bring higher economic benefits.
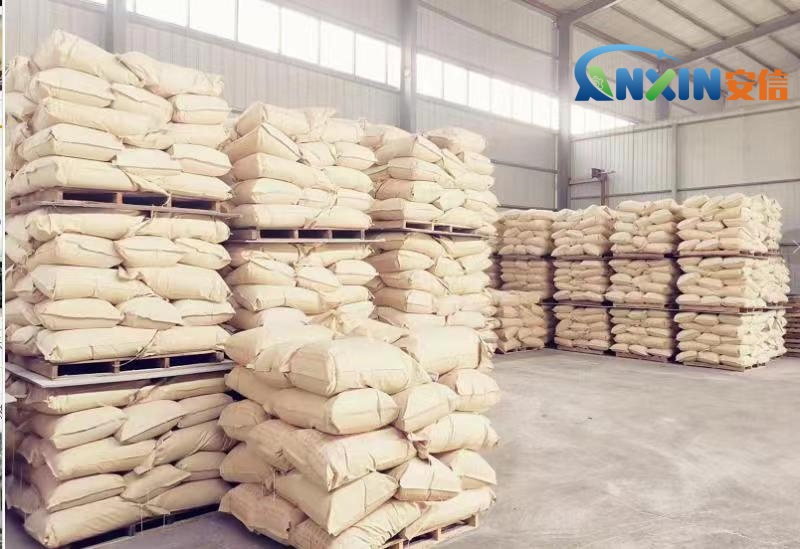
As a highly efficient chemical additive, CMC plays an important role in deep-sea drilling. It can not only enhance the performance of drilling fluid and improve the stability of wellbore, but also effectively inhibit the formation of hydrates, reduce environmental pollution, and improve operational efficiency and safety. With the continuous development of deep-sea drilling technology and the continuous improvement of environmental protection requirements, the application of CMC will become more extensive and become one of the indispensable key materials in deep-sea drilling.
Post time: Dec-21-2024