HPMC (Hydroxypropyl Methylcellulose) is a polymer chemical material commonly used in the construction industry. It is widely used in cement-based mortar, dry-mixed mortar, adhesives and other products to thicken, retain water, improve It has multiple functions such as adhesion and improved construction performance. Its role in mortar is particularly significant, especially in improving the crack resistance of mortar.
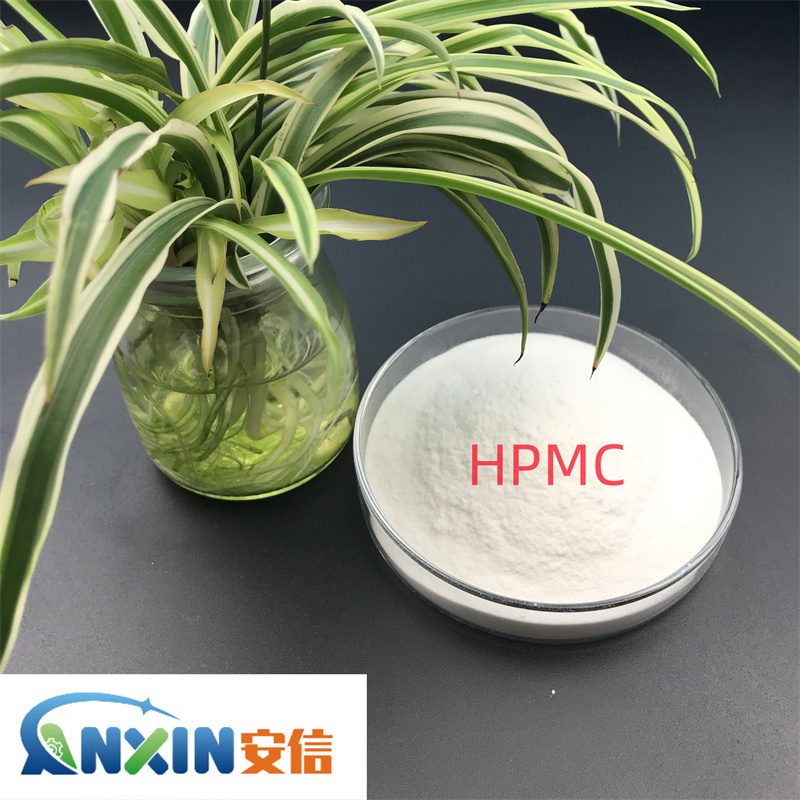
1. Enhanced water retention
HPMC has good water retention, which means that water will not evaporate too quickly during the mortar construction process, thus avoiding shrinkage cracks caused by excessive water loss. Especially in dry and high-temperature environments, the water retention effect of HPMC is particularly outstanding. The moisture in the mortar can remain relatively stable for a certain period of time to avoid premature drying, which is very critical to improving the crack resistance of the mortar. Water retention can delay the hydration process of cement, allowing cement particles to fully react with water over a longer period of time, thus enhancing the crack resistance of mortar.
2. Improve the adhesion of mortar
As a thickener, HPMC can form a good molecular network structure in the mortar to enhance the adhesion and fluidity of the mortar. This not only improves the bonding strength between the mortar and the base layer and reduces the cracking of the interface layer, but also improves the overall toughness of the mortar and reduces the occurrence of cracks caused by external forces during the construction process. Good adhesion makes the mortar more uniform during construction and reduces cracks caused by uneven thickness at joints.
3. Improve the plasticity and workability of mortar
HPMC improves the plasticity and operability of mortar, which can effectively improve the convenience of construction. Due to its thickening effect, HPMC can make the mortar have better adhesion and formability, effectively reducing the occurrence of cracks caused by uneven mortar and poor fluidity during construction. Good plasticity makes the mortar more evenly stressed during drying and shrinkage, reducing the possibility of cracks due to uneven stress.
4. Reduce shrinkage cracks
Dry shrinkage is the volume shrinkage caused by water evaporation during the drying process of mortar. Excessive dry shrinkage will cause cracks on the surface or inside of the mortar. HPMC slows down the rapid evaporation of water and reduces the occurrence of dry shrinkage through its high water retention and plasticity improvement effects. Research shows that mortar added with HPMC has a lower drying shrinkage rate and its volume changes less during the drying process, thus effectively preventing cracks caused by drying shrinkage. For large-area walls or floors, especially in hot summer or ventilated and dry environments, the role of HPMC is particularly important.
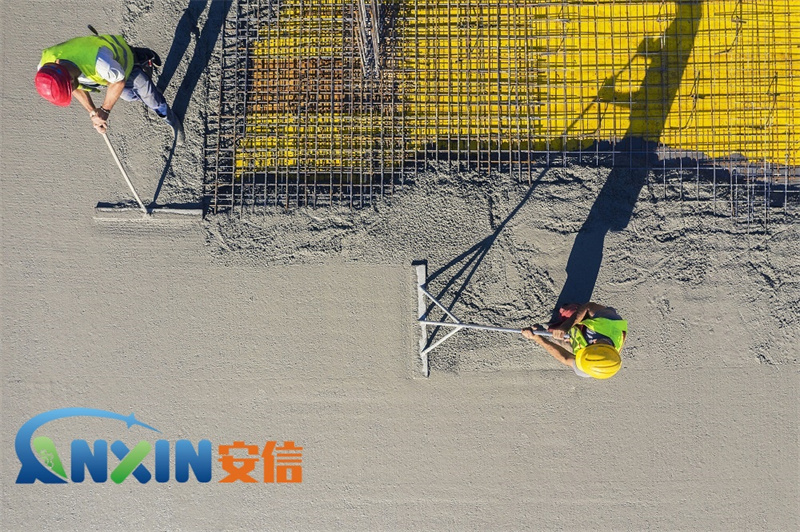
5. Improve the crack resistance of mortar
The molecular structure of HPMC can form certain chemical interactions with cement and other inorganic materials in the mortar, making the mortar have higher crack resistance after hardening. This enhanced cracking strength not only comes from the combination with HPMC during the cement hydration process, but also improves the toughness of the mortar to a certain extent. The toughness of the mortar after hardening is enhanced, which helps it withstand large external stress and is not prone to cracks. Especially in environments with large temperature differences or large changes in external loads, HPMC can effectively improve the crack resistance of mortar.
6. Increase the impermeability of mortar
As an organic polymer material, HPMC can form a microscopic network structure in the mortar to improve the compactness of the mortar. This characteristic makes the mortar more impermeable and reduces the permeability of moisture and other external media. In a humid or water-soaked environment, cracks on the surface and interior of the mortar are more likely to be invaded by moisture, leading to further expansion of the cracks. The addition of HPMC can effectively reduce the penetration of water and inhibit the expansion of cracks caused by water intrusion, thereby improving the crack resistance of the mortar to a certain extent.
7. Inhibit the generation and expansion of micro-cracks
During the drying and hardening process of mortar, micro cracks often occur inside, and these micro cracks may gradually expand and form visible cracks under the action of external forces. HPMC can form a uniform network structure inside the mortar through its molecular structure, reducing the probability of micro-cracks. Even if micro-cracks occur, HPMC can play a certain anti-crack role and prevent them from further expansion. This is because the polymer chains of HPMC can effectively disperse the stress on both sides of the crack through intermolecular interactions in the mortar, thereby inhibiting the expansion of the crack.
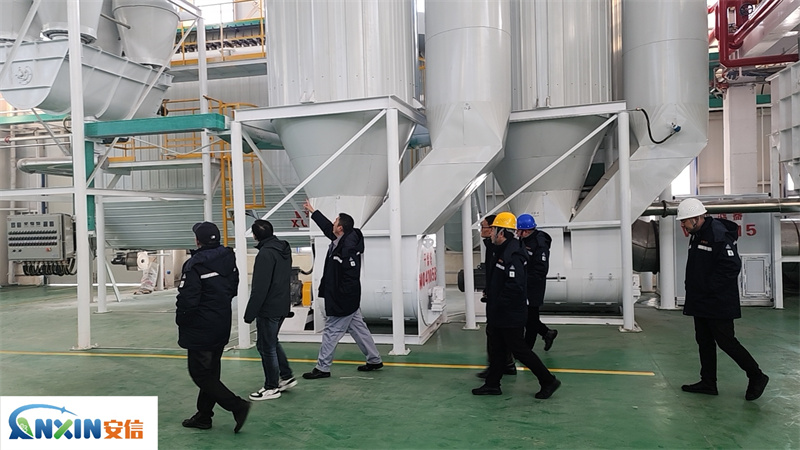
8. Improve the elastic modulus of mortar
Elastic modulus is an important indicator of a material's ability to resist deformation. For mortar, a high elastic modulus can make it more stable when subjected to external forces and less likely to cause excessive deformation or cracks. As a plasticizer, HPMC can increase its elastic modulus in mortar, allowing the mortar to better maintain its shape under the action of external forces, thus reducing the occurrence of cracks.
HPMC effectively improves the crack resistance of mortar in many aspects by improving the water retention, adhesion, plasticity and operability of mortar, reducing the occurrence of dry shrinkage cracks, and improving the crack resistance strength, impermeability and elastic modulus. performance. Therefore, the application of HPMC in construction mortar can not only improve the crack resistance of the mortar, but also improve the construction performance and extend the service life of the mortar.
Post time: Dec-16-2024