As a common building decoration material, caulking agent is widely used to fill gaps in floor tiles, wall tiles, etc. to ensure the flatness, aesthetics and sealing of the surface. In recent years, with the improvement of building quality requirements, the performance of caulking agent has been paid more and more attention. Among them, wear resistance, as an important performance indicator, has a direct impact on the service life and decorative effect of caulking agent. Hydroxypropyl methylcellulose (HPMC), as a commonly used natural polymer, is often used as a thickener, water retaining agent, rheology modifier, etc. in caulking agent. The addition of HPMC can not only improve the construction performance of caulking agent, but also improve its wear resistance to a certain extent.
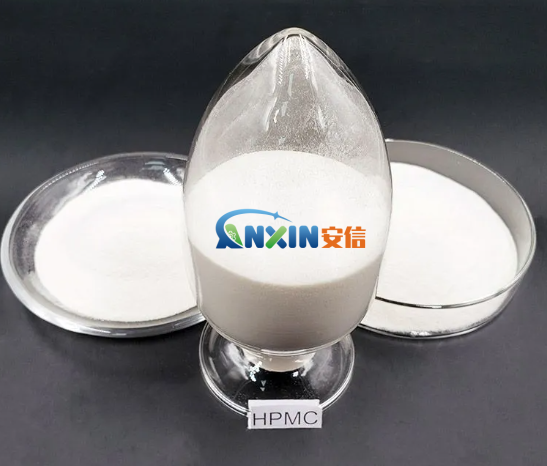
1. Basic characteristics of HPMC
HPMC is a polymer compound obtained by chemical modification of natural plant fibers (such as wood pulp or cotton), which has excellent water solubility and good biodegradability. As a thickener, HPMC can adjust the rheology of caulking agent and improve its workability during construction. In addition, AnxinCel®HPMC can also improve the water retention of caulking agents, avoiding cracks and falling off caused by premature water loss of caulking agents. Therefore, HPMC is widely used in adhesives, coatings, caulking agents and other products in the construction industry.
2. Wear resistance of caulking agents
Wear resistance refers to the ability of a material to resist wear under external forces. In caulking agents, wear resistance is mainly reflected in the fact that its surface is not easily damaged, peeled off or has obvious wear marks due to long-term friction. The wear resistance of caulking agents is crucial to the service life of gaps in floors and walls, especially in environments that are often exposed to mechanical friction or crowded with people, such as shopping malls, public places, kitchens, bathrooms and other areas. Caulking agents with poor wear resistance will lead to increased loss of materials in the gaps, affecting the decorative effect and may cause problems such as water seepage.
3. Effect of HPMC on the wear resistance of caulking agents
Improving the rheological properties of caulking agents
The addition of AnxinCel®HPMC can significantly improve the rheological properties of caulking agents. Its thickening effect makes the caulking agent have better construction properties, avoids the sag phenomenon caused by excessive dilution of the material during use, and enhances the bonding force of the caulking agent. In addition, proper thickening can also ensure the ratio accuracy of the caulking agent, so that it forms a uniform structure during the hardening process and reduces the probability of pores or cracks. These factors indirectly improve the wear resistance of the caulking agent surface, because the uniform and tight structure can better resist the action of external forces.
Improve the water resistance and water retention of the caulking agent
The water solubility and water retention of HPMC also play an important role in the wear resistance of the caulking agent. HPMC can effectively delay the volatilization of the caulking agent's water, ensure that the material maintains sufficient water during the hardening process, thereby improving its hardening density and strength. Higher strength helps the caulking agent surface better resist wear and reduce problems such as cracking, sanding and shedding caused by excessive water evaporation.
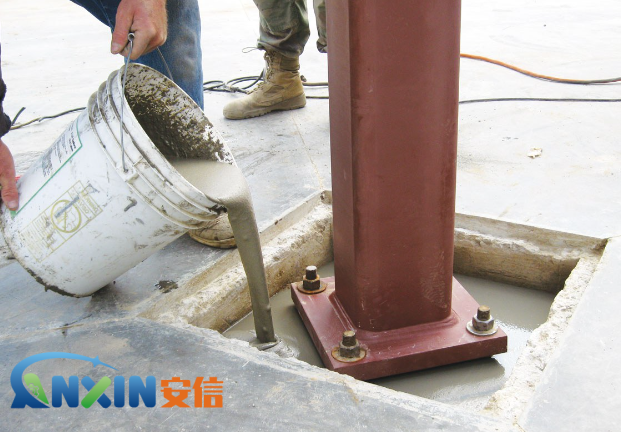
Form a stable network structure
The role of HPMC in the caulking agent is not limited to thickening. It can also form a stable network structure with other ingredients such as cement and gypsum. This structure can increase the density of the filler, making its surface harder and more wear-resistant. The network structure of the hardened filler can effectively withstand the impact of external forces such as friction and vibration, reducing surface wear. The stability of the network structure is closely related to the molecular weight and degree of substitution of HPMC. HPMC with a higher molecular weight and a moderate degree of substitution can provide stronger wear resistance.
Enhance the impact resistance of the filler
The elastic characteristics of AnxinCel®HPMC enable the filler to better disperse stress when it is impacted by external forces, avoiding cracks or fragments caused by excessive local stress. This impact resistance is closely related to wear resistance, because during the friction process, the surface of the filler may be subjected to a small impact force, increasing the risk of material wear. The addition of HPMC enhances the toughness of the filler, making it less likely to break under friction.
4. Optimization strategy of HPMC on the wear resistance of the filler
In order to further improve the wear resistance of HPMC in the filler, researchers and engineers can optimize from the following aspects:
Select appropriate HPMC varieties: The molecular weight and degree of substitution of HPMC have a direct impact on the performance of the filler. HPMC with a higher molecular weight usually has better thickening effect and rheological properties, but too high a molecular weight may lead to reduced construction properties. Therefore, when selecting materials, it is necessary to select the appropriate HPMC variety according to the requirements of the specific application scenario.
Adjust the amount of HPMC added: The appropriate amount of HPMC can improve the wear resistance of the caulking agent, but excessive addition may cause the surface of the caulking agent to be too hard and lack sufficient elasticity, thereby affecting its impact resistance. Therefore, it is necessary to determine the optimal amount of HPMC added through experiments.
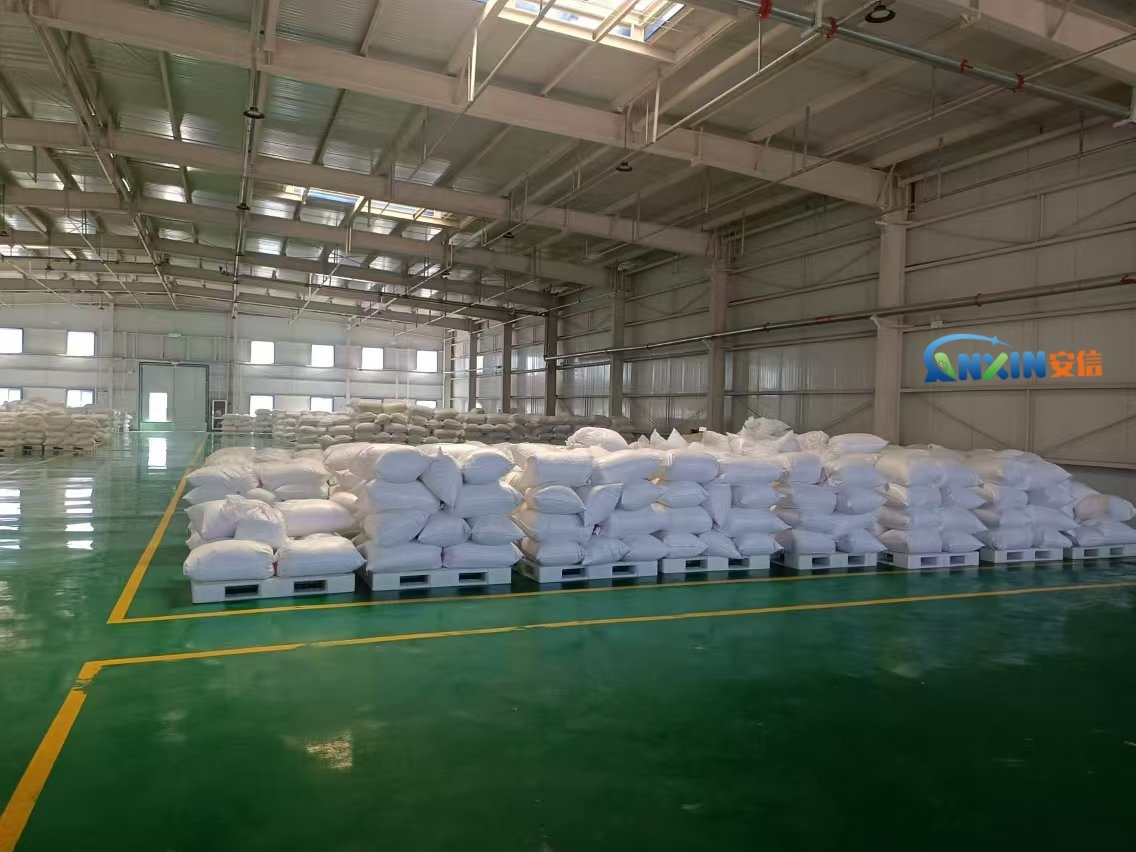
Compatibility with other ingredients: On the basis of HPMC, adding some fillers such as reinforcing fibers and nanomaterials can further improve the wear resistance of the caulking agent. For example, materials such as nano-silicon and nano-alumina can form a microscopic reinforcing structure in the caulking agent, significantly improving its surface hardness and wear resistance.
As an important additive in the caulking agent, HPMC can significantly improve its wear resistance by improving the rheological properties, water retention, hardness and impact resistance of the caulking agent. By rationally selecting the type and amount of AnxinCel®HPMC, combined with other optimization measures, the service life of the caulking agent can be effectively extended to ensure its good performance in various complex environments. With the continuous improvement of the performance requirements of building materials, the application prospects of HPMC in caulking agents are broad and worthy of further research and development.
Post time: Jan-08-2025